Battling Complacency the Workplace
Author: Sensori Safety Published: 1/03/2022 Time: 3 Minutes
Complacency affects every workplace and employee to a different degree. It can often show up as a false sense of security which leads to a lack of awareness of your surroundings. This can be anything from letting your guard down and losing focus, to not actively looking for hazards. A complacent mindset is the most dangerous presence in the workplace.
Complacency can be viewed as an inaccurate perception of risk. The more you do something with nothing adverse happening, the more secure you begin to feel, thinking that you can complete the task without consequence. However, too much familiarity with a hazard can breed complacency.
Complacency can put a person in “auto-pilot” mode, causing them to move step by step without thinking critically about their actions. This can increase the potential for risks and injuries, and it can happen regardless of age or experience. Whether it’s the result of spending too much time on a task or getting too comfortable with a daily routine, we can all work to minimize the risk of becoming complacent.
Think about how many times you have driven a car and gotten to your destination without realizing how you got there or what route you took. Think about how many people continue to text and drive knowing the hazards associated with their actions, or how many team members use the stairs without utilizing the safety handrails. Complacency is present in more places than we realize.
Too often you do not notice how complacent you’ve become until you have had a near miss or a close call. Though this can grab your attention for some time, it can be easy for someone to become complacent once again, at least until an injury occurs.
The fact is that injuries, big or small, are difficult to prevent with compliance alone. This is because they are largely the result of worker actions that are often fueled by complacency and other human factors leading to unintentional errors. Awareness, safety training, and safety protocols alone, cannot win this battle. We must assess, analyze, and measure the human factors that lead to inattention and worker complacency.
In 2021, we conducted a vision and neurocognitive training research study due to employers experiencing high numbers of mobile equipment incidents. After the training drill, it was determined that the operator's Left-Hand Peripheral Field of Vision was 274ms slower than their Left-Hand Central Field of Vision. It was also determined that the operator's Right-Hand Peripheral Field of Vision was 424ms slower than their Right-Hand Central Field of Vision. This indicates a significant difference in reaction time with Peripheral Field of Vision drills yielding longer reaction times than Central Field of Vision drills.
With respect to Central Field of Vision drills only, the Right-Hand drills took 164ms longer in reaction time than the Left-Hand drills. This indicated that although the Right Hand is the subject's dominant hand, it was 164ms slower than the left hand.
- Left Hand Central Field of Vision 695.79ms
- Right Hand Central Field of Vision 859.55ms
Regarding Peripheral Field of Vision drills only, the Right-Hand drills took 314ms longer in reaction time than the Left-Hand drills. This indicated that the Right Hand was 314ms slower than the left hand, although the Right Hand is the subject's dominant hand.
- Left Hand Peripheral Field of Vision 969.38ms
- Right Hand Peripheral Field of Vision 1283.06ms
What we can tell from the data is that overall, the subject's central field of vision yields faster reaction time than their peripheral field of vision. In comparison to left and right vision (both central and peripheral), the subject has a slower reaction time on the right side, although this is their dominant side/hand.
This may indicate that a member's dominant hand/side of the body may have a slower reaction time than expected, which may be contributed to the familiarity that comes with the use of a dominant/frequently used hand. It is important to note that these slower reaction times with the dominant hand could indicate complacency.
Complacency is a common contributor to unintentional injuries. When workers get overly comfortable with a procedure, they’ll often mentally minimize the amount of risk involved. Complacency can then be exacerbated by a belief that rules and regulations form an infallible safety net. However, the good news is that with our Safe Sight Vision training program for mobile equipment operators, this can be both measured and monitored.
If you are looking to reduce worker complacency we can help. Sensori Safety was created to provide preventative services to assess, analyze, measure, and train the operator’s vision performance; helping employers understand the operator’s speed, accuracy, depth perception, peripheral awareness, and hand-eye coordination.
If you enjoyed this reading, please feel free to join our online community. Comment, share, and contact us today if you are interested in learning more about our services. For more information regarding the details of this study please feel free to contact us today or join the community to get access to the full report.
#SensoriSafety #VisionTraining #VisionTesting #ForkliftOperator #CraneOperator #manufacturing #construction
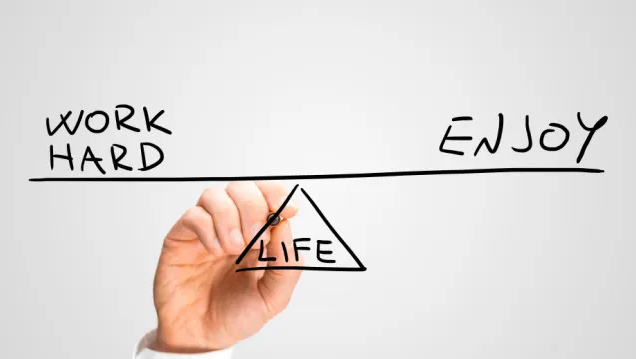
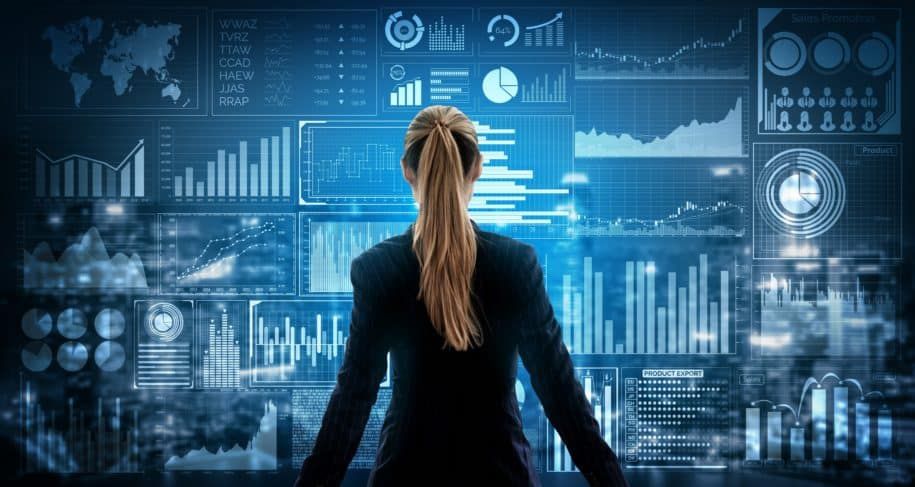
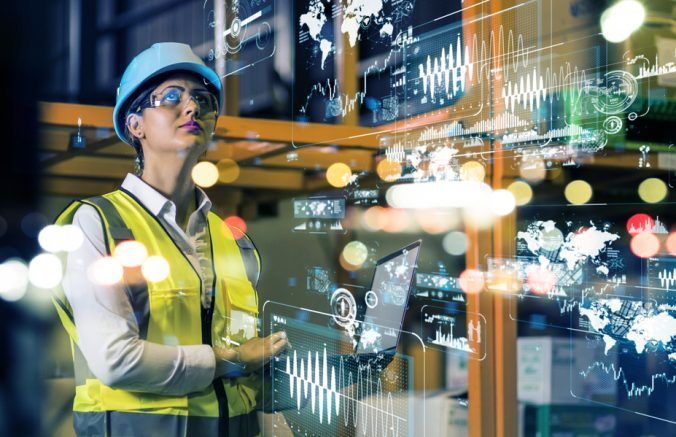

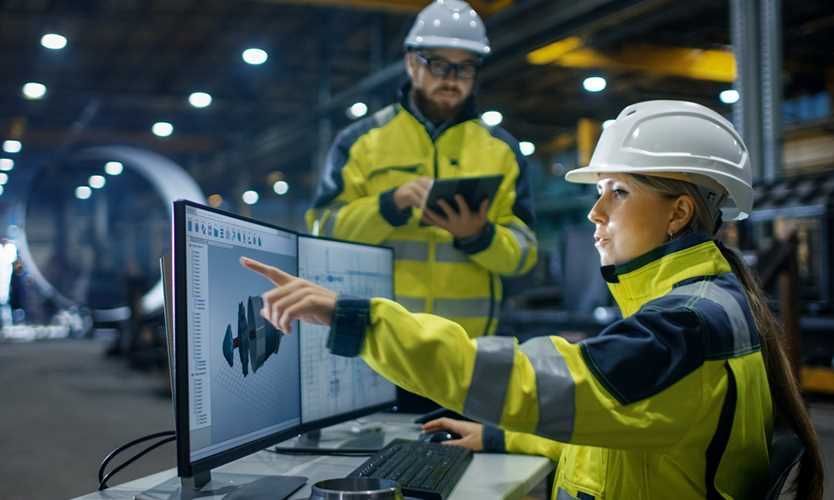